How do we protect valuable assets from the risk of fire?
Room integrity testing plays a critical part in mitigating this risk. A fire within your company building could have serious business ramifications, so we are all used to operating in a way that reduces fire-risk when at work.
Sprinkler systems and fire extinguishers can protect lives by releasing water at the site of fires. But when it comes to protecting the most valuable equipment in a building, water can cause as much damage as a fire, so a different approach must be used.
This approach is known as Gaseous Fire Suppression, which can work in one of two ways.
- By displacing some of the Oxygen by releasing an inert gas into the enclosure, i.e Argon, CO2 or IG-55
- By reducing the heat of the fire and thereby reducing or stopping the chain-reaction across the enclosure, i.e Novec 1230 and FM-200
Proving the System Will Work
The suppression system is usually designed to work for 10 minutes (this is called the Hold Time), to give enough time for emergency services to respond. As such, the concentration of the gas must be maintained above a defined percentage for the required hold time.
A good way to imagine why it is called a Hold Time it is to not think of it as a gas, but to imagine filling the enclosure to the top with water, and you want 90% of the water to stay there for 10 minutes. If the enclosure has a lot of holes, then the water is going to leak out rather quickly. If it is airtight, or watertight, then you will have most or all that water left at the end of the 10 minutes.
Air Tightness Testing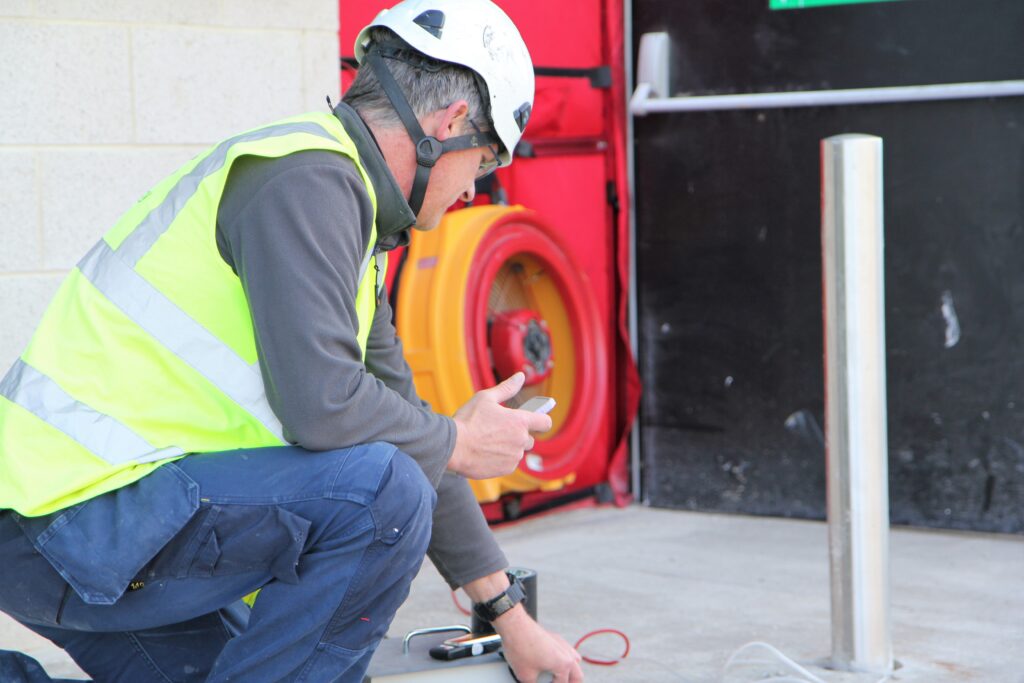
For this Hold Time, we need to demonstrate some level of airtightness. This is known as room integrity testing and for many insurances, this does need to be done every 12 months after the construction.
The required level of airtightness does differ greatly, depending on the type of gas, the size of the enclosure, the height of the equipment, as well as many other factors. Even having fans operating in the enclosure will change the way the system works, so it is much more complex than a normal airtightness test.
With the correct gas and enclosure information, your test engineer will be able to give an estimate of the required level of airtightness and advise you accordingly. When planning any of these projects, it helps to get a air tightness consultant involved at an early stage as the construction may need to change based on the information given.
As an example, one such project we have worked on required an equivalent air tightness of 0.5m3/h.m2, which is tighter than some of the most energy-efficient buildings you will come across, so this required a very different approach to the construction.
The Testing Procedure
Room integrity testing involves a calibrated fan setup like a normal airtightness test, but there does need to be a pressurisation and a depressurisation result to adhere to the methodologies of BS EN 15004 and NFPA 2001.
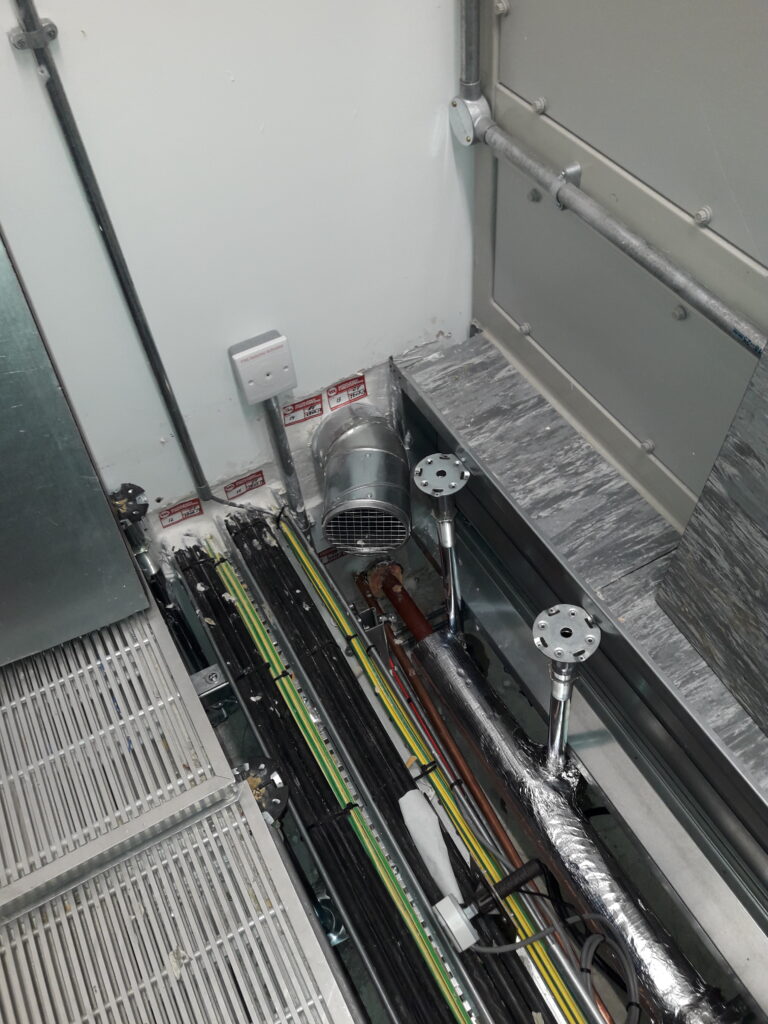
Cable penetrations in a data centre
One important distinction, is that no temporary sealing can be made to any element of the enclosure during the test. This test needs to demonstrate how the gas will perform under normal working conditions, so all vents and air handling units must be open and operating as normal.
There is another highly important aspect that must be considered as part of this test….
Peak Pressure Analysis
If you release 100kg of gas into an airtight enclosure over 30 seconds, there will be a significant amount of pressure created. This could be well over 2,000 Pa in some circumstances, which would damage entrance doors, and even destroy the enclosure completely if the walls are not able to support that level of pressure.
To reduce this pressure, you will have Pressure Relief Vents (PRVs) installed in the walls, ideally at a high level. An important part of the test that we perform will be to work out this peak pressure and then demonstrate that these vents provide enough of a pressure reduction.
This involves a second set of tests where the enclosure if pressurised to 125 Pa, at which point the vents should be fully open. The vents are then fixed in this position and the effective leakage area is then worked out using another airtightness test. We will advise if the PRVs meet your requirements.
Strategies for Getting a Pass
It is firstly critical to establish how airtight the enclosure/room needs to be, using the installation details for the suppression system and the building geometry. The earlier this is done, the better as this information can determine a good sealing strategy, or even suggest that a system redesign is needed.
- Large trunks of data cables are common areas of failure. The ideal solution is to lay a bead of mastic at the opening, then sit some of the cables into it in a way that means they are not touching. The mastic should be allowed to dry, and the process can be repeated by applying another bead of mastic and then sitting more cables into it. The result should be an effective seal around each cable that would otherwise have been very difficult to achieve.
- Plasterboard should be well sealed at the head and beneath the raised access floors as a continuous line. Take care to get a good seal at difficult junctions.
- Exposed Blockwork should be plastered or have received several coats of paint.
- Cable penetrations behind control panels and electrical fittings must be sealed during the installation, so that there is no need to remove these at a later stage for remedial works.
- Cable trays can be difficult to seal when in a Raised Access Floor. Brief the contractors during the installation that these need a good seal beneath them, and for each individual cable to have a complete seal around it.
- Pressure Relief Vents normally do present some leakage when closed. If the requirements of the enclosure are tight, then higher quality vents may be needed to give the best chance of passing.
- Conduits should be sealed as they penetrate the perimeter wall and should also be sealed inside. This can be difficult to do during remedials, and so should be done during the installation before the conduit is closed.
- Ductwork penetrations will need to be sealed, with the main difficulty being any sections that are flush against a wall or floor slab. This is a detail that is easily missed, so ensure that the contractor is aware of the importance of sealing these areas at an early stage.
Partner with Build Energy for Your Project
We have vast experience in the testing of controlled environments and can help you deliver successful outcomes in your scheme. Contact us today at on 0330 055 34 05 or email us at be@buildenergy.co.uk. Our expert consultants are here to help.